离心泵
这个过程工业的工作马提供了一个最大的机会节能.
在指定泵时,设计过程通常是保守的,特别是在计算所需的排放压力时。因此,通过排放控制阀的压降通常比过程控制所需的高(有时高得多)。
很多,如果不是大多数的话离心泵在石油、天然气和石油化工行业中,必须满足API - 610规范或同等要求。守则的主要功能是确保安全可靠的运作。泵是否有效运行,主要是工程师做出选择的责任。
以典型的单级离心泵为例,选择图如图8.2所示。
显然,理想的情况是使泵达到最大值叶轮大小和操作在流量对应的最佳效率点(BEP)。但通常选用较小的叶轮(一般在尺寸范围的1/3 ~ 2/3之间)。同时,设计工作点选择在BEP的左侧。这两项决定都是为未来扬程和流量的升级提供可能,与工厂消除瓶颈相关,而无需更换泵。还要注意的是,泵扬程包括通过排放控制阀的压降余量。
总的来说,消耗的能量很容易比可实现的最小值多20%。
最好的办法是尽量减少泵能源消耗现有机组的一种方法是为机匣拟合最大叶轮尺寸并转换为变频
最大叶轮尺寸曲线
最大叶轮尺寸曲线
-
- 叶轮推荐尺寸
流
图8.2泵选型图
图8.2泵选型图
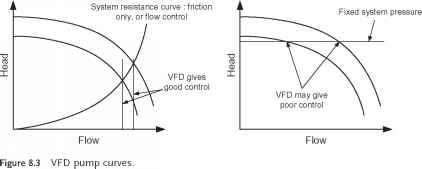
变频器(VFD)。泵速由所需的过程控制参数——流量、滚筒液位、压力等决定。这消除了控制阀的压力损失。如果没有控制阀,速度也会降低,因此轴承和密封寿命也会提高。一些操作人员将控制阀留在原位——全开,但如果检测到故障,VFD系统默认为全速,则将其设置为运行。
VFD的应用必须小心。如果泵入由摩擦定义压降的系统(例如传输管道),VFD是理想的。然而,如果泵入固定压力系统,那么根据泵头流曲线的形状,速度的微小变化会对流量产生很大的影响,在设计控制系统时必须谨慎。在这种情况下,VFD可以连接到泵吸收能力以避免不稳定(图8.3)。
还有一个问题需要避免。如果转速控制设置在太紧的范围内,那么传递扭矩的突然和持续变化可能导致联轴器故障甚至轴故障。尽管这种情况很少见,但经历过这种问题的工程师不愿应用vfd,从而失去了节能的机会。
如果两台泵并联运行,则VFD只能与单个泵的流量计量一起使用,以确保负荷分担。如果流量不是控制参数,这将变得复杂,因此很少使用成对运行泵的VFD。
当该系统应用于与汽包液位相连的锅炉给水泵时,具有相当大的节能潜力。在很长一段时间里,“规则”是泵的排放压力应该足够高,使水随着鼓的安全阀吹进鼓里。因此,在这种情况下,泵排气压力通常比VFD所需的压力高50%。
离心泵通常规定具有从工作点到截止点(零流量)连续上升的扬程流量曲线。这样做是为了稳定,因为在相同的压力下,上升-下降曲线可以有两个工作点(图8.4)。
对于高扬程、低容量的泵,最有效的叶轮设计结果是上升-下降曲线。为了得到连续上升的曲线,需要减小叶轮叶片的出口角。这降低了效率和扬程,由于在叶轮通道的速度较高,因此需要一个更大直径的叶轮。(注意:这是指传统的叶轮加蜗壳设计,而不是使用不同原理的Barske类型。)
通过确保控制系统将流量保持在曲线峰值头的右侧,可以采用更有效的设计。由于这种类型的泵需要一个更小的叶轮,还有一个额外的好处,即节省成本,因为壳体尺寸也更小。
对于新的安装,有理由增加叶轮直径并以较低的速度运行。叶轮通道中流体速度的降低提高了效率。
两种可能的流量在同一排放头
两种可能的流量在同一排放头
-
- 最佳效率点
继续阅读:单级涡轮
这篇文章有用吗?